CASE STUDY
Transforming Safety in Steelmaking Through HOP Principles: A Client Success Story
Industry: Steelmaking
What happens when a leading steel manufacturer rethinks everything it knows about workplace safety? This case study tells the story of a company that moved beyond traditional, compliance-driven safety measures to build a culture where learning, innovation, and leadership thrive.
💬 "A program like this is overdue. If I had an opportunity to participate as a new branch manager, it would have eased the transition into the safety culture of our business and assisted significantly in managing the systems, language and approach to the Branch Manager role.”
Services
-
Human and Organisational Performance (HOP) Integration
-
Learning Teams Implementation
-
Safety Culture Maturity Uplift
-
Strategic Safety Program Design & Facilitation
-
Custom Learning Material & Program Design
-
Program Success Measurement & Reporting

Client Background
Operating across North America, Australia, New Zealand, the Pacific Islands, and Asia, this organisation had long prioritised health and safety. Yet, their legacy Behavioural-Based Safety (BBS) approach had its limits - reactive risk management and a focus on compliance weren’t enough to create lasting change. Recognising the need for a shift, they partnered with us to embed Human and Organisational Performance (HOP) principles into their leadership training.
The Results?
-
Leaders now have genuine ownership over safety decisions.
-
Safety culture has become more collaborative and transparent.
-
They’ve introduced Learning Teams and psychosocial risk assessments across the organisation.
-
The post-program self-assessments show measurable improvement in key safety areas.
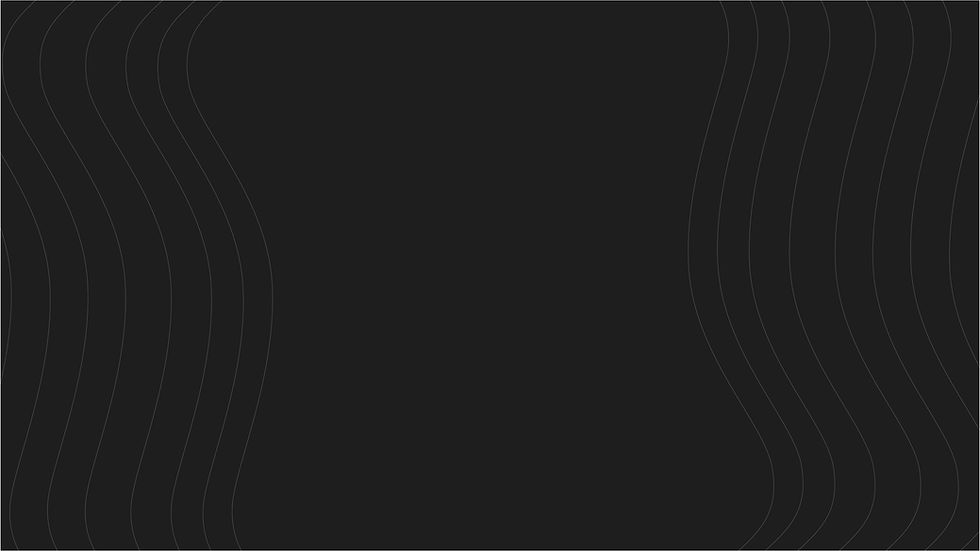
📥 Grab the full case study
Enter your details below to receive the case study in your inbox.
Grab the full case study